POTTING PROJECTS RARELY FIT THE STANDARD MOLD
Efficient, tailored adhesive bonding and potting processes have a major impact on the performance of electrical components in the long run. Even the slightest deviations or inhomogeneities in the dispensing and potting processes can significantly compromise the quality and service life of components. Determining which potting or application process is the right one for a particular task depends on a number of factors. In addition to the workpieces themselves, the materials used, the user potting requirements, the potting properties, and the integration of adhesive bonding, dispensing and potting processes into the production environment play an important role.
But regardless of the adhesive bonding or potting task, thanks to over 30 years of experience, we can always provide you with the best and most cost-effective solution.
Where is dispensing technology used?
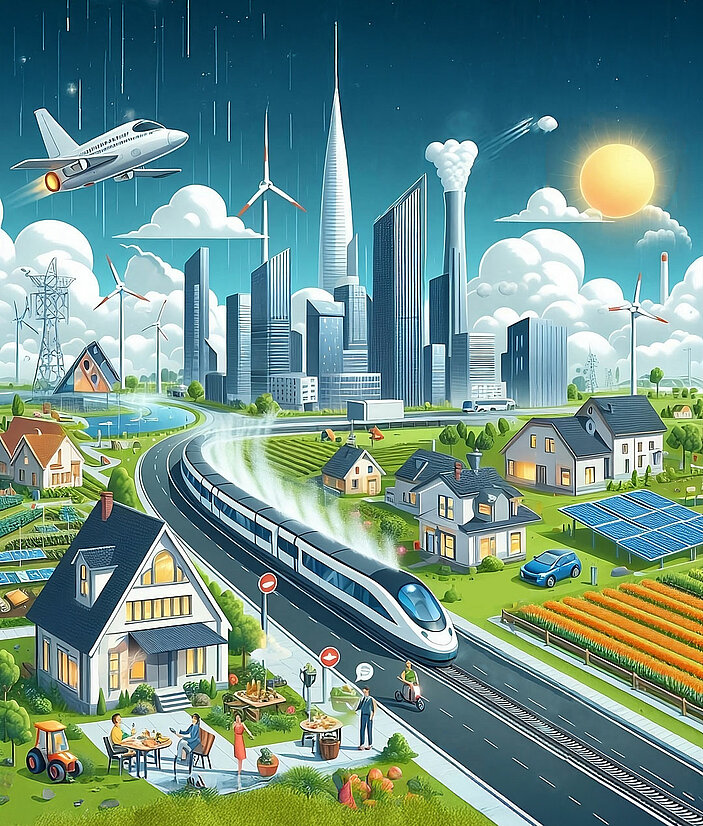
Electric toothbrushes
The electronics of the drive unit are protected by atmospheric potting. The low-viscosity material envelops the sensitive components, shielding them from vibrations and moisture.
E-scooters
The battery unit in an e-scooter is protected by potting material, safeguarding it from water and shocks. This ensures safe operation even under harsh conditions.
Trains
The windings in the stator of a train drive are fully potted to ensure efficient heat dissipation and electrical insulation.
Space shuttle
Seals for electronic components onboard are applied using dispensing technology to protect them from extreme vibrations and external influences during rocket launches.
Air taxis
Sensors, electronic control units, and battery management systems must be reliably protected against moisture, dust, and vibrations. Bubble-free potting with low-viscosity materials, along with the precise application of potting resins, enhances the durability and functional reliability of these components.
Laptop
The fieldbus connectors linking the laptop to the docking station are potted to protect them from moisture and mechanical stress.
Camera systems
The lens of an industrial camera system is secured and sealed with specialized materials to protect it from dust, vibrations, and moisture.
Agriculture
The control unit of a tractor is protected with potting materials to shield it from wind, weather, and extreme temperatures. The applied sealing materials act as a barrier against external influences and, when using specialized adhesives, also serve as bonding elements.
Wind turbines
The IGBTs (Insulated Gate Bipolar Transistors) in wind turbines are potted bubble-free under vacuum to ensure their functionality under high loads.
Electric cars
The battery management system (BMS) in an electric vehicle is potted to protect the sensitive electronics from shocks, heat, and moisture.
Blood glucose monitors
The semiconductor chips on the circuit board of a blood glucose meter are protected by glob tops to shield them from environmental factors and mechanical stress.
Heat pumps
The drive module of a heat pump is potted with polyurethane (PU) under vacuum. The bubble-free potting protects the stator board with its ignition coils while ensuring optimal thermal conductivity.